A machining center is a highly automated CNC machine tool that performs a wide variety of manufacturing processes, such as milling, drilling, tapping, and boring, all in a single setup. Thanks to automatic tool changers and advanced control systems, machining centers dramatically improve production efficiency and precision in modern manufacturing.
Whether you’re producing aerospace components, automotive parts, or complex molds, choosing the right machining center can transform your productivity.
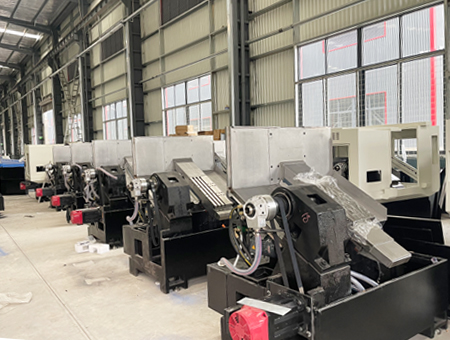
What Is a Machining Center?
A machining center is an advanced form of CNC (Computer Numerical Control) milling machine equipped with multiple features for high-precision and multi-process metalworking.
Key characteristics include:
- Automatic Tool Changer (ATC)
- Tool Magazine for holding various tools
- High-speed Spindles
- Rigid Structure to ensure machining stability
- Computer Control System (e.g., FANUC, Siemens, Mitsubishi)
Unlike traditional milling machines, machining centers can perform multiple tasks without manual setup changes, making them ideal for both small-batch customization and large-scale production.
Main Types of Machining Centers
Depending on spindle orientation and axis configuration, machining centers come in several types:
🔹 1. Vertical Machining Center (VMC)
- Spindle is vertically oriented
- Ideal for flat parts and mold processing
- Compact footprint, easy to operate
- Common in mold, electronics, and automotive industries
🔹 2. Horizontal Machining Center (HMC)
- Spindle is horizontally oriented
- Suitable for heavy and complex parts
- Better chip evacuation and stability
- Often used in automotive and aerospace industries
🔹 3. 5-Axis Machining Center
- Simultaneous 5-axis movement (X, Y, Z + A, B/C axes)
- Can machine complex surfaces and deep cavities in one setup
- High-end solution for aerospace, medical, and high-precision components
🔹 4. Gantry Machining Center (Bridge-Type)
- Large working area, double-column support
- Used for large dies, structural parts, or energy equipment
- Excellent rigidity and load-bearing capacity
Key Components and Features
Component | Description |
---|---|
Spindle | Determines cutting speed and power |
ATC System | Enables fast automatic tool changes |
Guideways | Linear or box ways influence stability and speed |
Control Unit | CNC system for programming and real-time control |
Chip Conveyor | Automatic chip removal for clean operation |
Optional features:
- Coolant through spindle (CTS)
- Probing systems for tool & part detection
- Enclosure and dust protection for clean-room needs
Applications of Machining Centers
Machining centers are widely used in industries including:
- Automotive: engine parts, gearboxes, aluminum housings
- Aerospace: turbine blades, structural components
- Medical: orthopedic implants, surgical tools
- Mold Making: injection molds, die casting molds
- Electronics: precision casings, heat sinks
- Energy: wind turbine hubs, valve bodies
Their versatility makes them indispensable for both high-mix, low-volume production and automated mass manufacturing.
Benefits of Using a Machining Center
- 🔧 Precision and Consistency across multiple operations
- ⏱️ Reduced Setup Time with tool changers and probing
- 💰 Lower Labor Cost due to automation
- 📈 Increased Throughput and repeatability
- ♻️ High Flexibility for prototyping and custom orders
🔍 Need Help Choosing the Right Machining Center?
Contact our team today for expert consultation, machine catalogs, and free layout proposals. Whether you’re expanding your factory or upgrading to a smarter CNC solution, we’re here to support your growth.