As a core tool in modern manufacturing, the CNC mill is widely used for high-precision part machining. Whether in aerospace, automotive, medical devices, or consumer electronics, precise CNC milling ensures product quality and performance. This article will explore the concepts of CNC milling machine accuracy and tolerance, how to ensure optimal machining results, and the key factors in selecting the right equipment and optimizing the machining process.
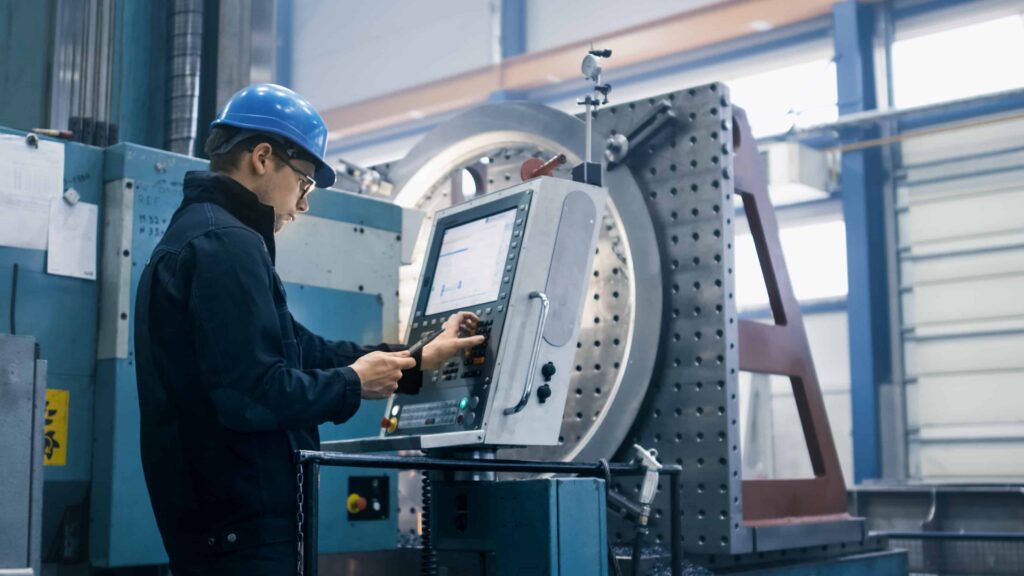
1. Understanding CNC Milling Machine Accuracy and Tolerance
Definitions of Accuracy and Tolerance
- Accuracy: Accuracy refers to the degree of closeness between the machined part’s actual dimensions and the design dimensions. The higher the accuracy, the smaller the deviation between the actual and target values.
- Tolerance: Tolerance is the permissible deviation range for the dimensions of a part during the manufacturing process. It defines the maximum and minimum dimensions that are acceptable to ensure the part fits with other components.
Why Are Accuracy and Tolerance Crucial?
Accuracy and tolerance are critical in any industry requiring high-performance parts. In high-precision fields such as aerospace, medical devices, and precision machinery, even the smallest deviation can cause part failure, reduce product quality, and compromise reliability. Therefore, ensuring the accuracy and tolerance of a CNC mill directly impacts the success of the product.
2. How to Achieve High Accuracy with CNC Mills?
Key Factors for Achieving High Accuracy
- High Rigidity Machine Structure: The frame and components of a CNC mill must have sufficient rigidity. High rigidity helps reduce vibrations during the machining process, ensuring that the cutting tool remains stable, thus maintaining machining accuracy.
- Precision Guides and Ball Screws: The guides and ball screws in a CNC mill play a crucial role in achieving high-precision movement. High-quality guides and ball screws significantly reduce friction, which improves machining accuracy.
- High-Precision Spindle: The spindle in a CNC mill directly affects the stability of the cutting process. A high-precision spindle reduces radial errors, ensuring better machining accuracy.
Role of CNC Control Systems and Technology
Modern CNC mills are typically equipped with advanced control systems that precisely control the tool’s path and speed. Some high-end machines use closed-loop control systems, which continuously monitor and adjust the position and speed of the machine to maintain accuracy. Combined with efficient CAD/CAM software, design and programming can achieve highly precise part manufacturing.
3. Choosing and Optimizing Tolerances
How to Select the Appropriate Tolerance Based on Needs?
- Standard vs. Tight Tolerances: For parts that do not require high precision, a larger tolerance range can be used, which often lowers machining costs. However, for parts requiring high precision, tighter tolerances must be selected to ensure the functionality and quality of the part.
- Functionality-Driven Tolerance Selection: For example, parts involved in mechanical fits require very tight tolerances to ensure smooth operation and durability. Decorative parts may allow for more relaxed tolerances.
Material Characteristics and Tolerance
- Material Hardness: The hardness of different materials can impact the machining process and the required tolerances. For example, harder materials such as steel may require special tools to minimize errors during cutting.
- Thermal Expansion and Contraction: During CNC milling, the generation of heat may cause materials to expand or contract, affecting tolerance. High-precision machining requires controlling temperature fluctuations during the process.
4. How to Optimize CNC Mill Accuracy During Machining?
Equipment Maintenance and Calibration
- Regularly calibrating the CNC mill is the first step in ensuring accuracy. Over time, machine parts may wear or deform, affecting machining precision. Regular checks and calibration ensure the equipment stays in optimal condition.
- Cleaning and Lubrication: Keeping the CNC mill clean prevents metal shavings and dust from accumulating, which could damage precise components. Additionally, proper lubrication helps reduce friction and improve machining accuracy.
Tool Management
- Tool Selection: Choose the appropriate cutting tool based on the material being machined, part shape, and size. The right tool not only improves machining accuracy but also extends tool life.
- Tool Wear Monitoring: Tool wear can lead to irregularities in the cutting process, impacting machining accuracy. Therefore, regularly checking and replacing tools is crucial for maintaining high precision.
Optimizing Machining Parameters
- Feed Rate and Cutting Depth: Setting the feed rate and cutting depth appropriately is essential, as excessive feed rate or cutting depth may lead to errors. These parameters should be adjusted based on material and machining requirements.
- Use of Coolants: Coolants reduce cutting temperatures and improve tool life, while also mitigating thermal expansion effects, which can influence machining accuracy.
5. Common Accuracy Issues and Solutions
Errors Caused by Vibration
- Solution: Ensure the CNC mill is stable and avoid unnecessary vibrations. This can be achieved by increasing the machine’s weight, optimizing part clamping, and adjusting cutting parameters to reduce vibrations.
Thermal Deformation
- Solution: Control the temperature of the machining environment and use cooling systems to reduce thermal expansion in the workpiece and tool, ensuring accuracy.
Tool Wear
- Solution: Regularly monitor tool conditions and replace or regrind tools when wear becomes significant. Using the right tools for specific materials can minimize wear.
6. Conclusion
In CNC milling, managing accuracy and tolerance is crucial for ensuring the quality of parts. By selecting the right equipment, optimizing machining parameters, maintaining the CNC mill regularly, and paying attention to tool usage and replacement, high accuracy and consistency can be achieved during the machining process. With ongoing technological advancements, CNC mills continue to evolve, offering more efficient and precise machining solutions for various industries.